Market needs change daily, which means services or products also have to be adapted quickly. Regardless of agility level, specific structural guidelines within a process can be valuable in approaching such needs with a certain level of professionalism. One concept that stands out in this regard is the PDCA cycle. In this article, we will tell you how it works, how it can help your company, and whether it is suitable for quick success.
Also known as the Deming circle or Deming cycle, the PDCA cycle is a concept for achieving a continuous improvement process, both in product development and in root cause failure analysis. The PDCA cycle is made up of a continuous loop of four stages: Plan, Do, Check, and Act. The particular strength of the PDCA cycle lies in its ease of application. The cycle is designed for long-term use and is intended to improve a company’s quality management instead of simply achieving short-term success.
The origin of the PDCA cycle dates back over 400 years to the time of Galileo and Francis Bacon, who were known for their application of inductive reasoning. The form we know today was developed by physicist Andrew Shewhart in the 1930s, under the name the Shewhart cycle. It was then further developed by W. Edwards Deming and used by Japanese companies, among others, during reconstruction following World War II.
The difference between PDCA and PDSA
In addition to the PDCA cycle, there is also a similarly sounding approach: the PDSA cycle. In this case, the “Check” stage is replaced with “Study.” This can be traced back to Deming, who rejected the “Check” stage because he saw it as a misunderstood modification of his idea. For him, it was not about creating a comparison between the current and target state. Instead, he was more concerned with learning from the obtained analyses and, as a result, sustainably improving the quality of the process. In his mind, the method could be illustrated using a spiral rather than a circle that is constantly spinning.
The four stages of the PDCA cycle are set in stone and do not change.
- Plan
Within this stage, the analysis of both the current and desired state takes place. During this time, areas of improvement are identified and corresponding actions that should lead to the achievement of the desired goal are derived.
- Do
Subsequently, the pre-planned actions are implemented into the appropriate departments.
- Check
The results of the actions are then evaluated to determine whether or not they led to achievement of the defined goal.
- Act
If the actions led to a satisfactory result, they become standard practice for the future. Activities that did not lead to—or not sufficiently lead to—the desired goal are used as starting points to repeat the cycle until the goal is achieved.
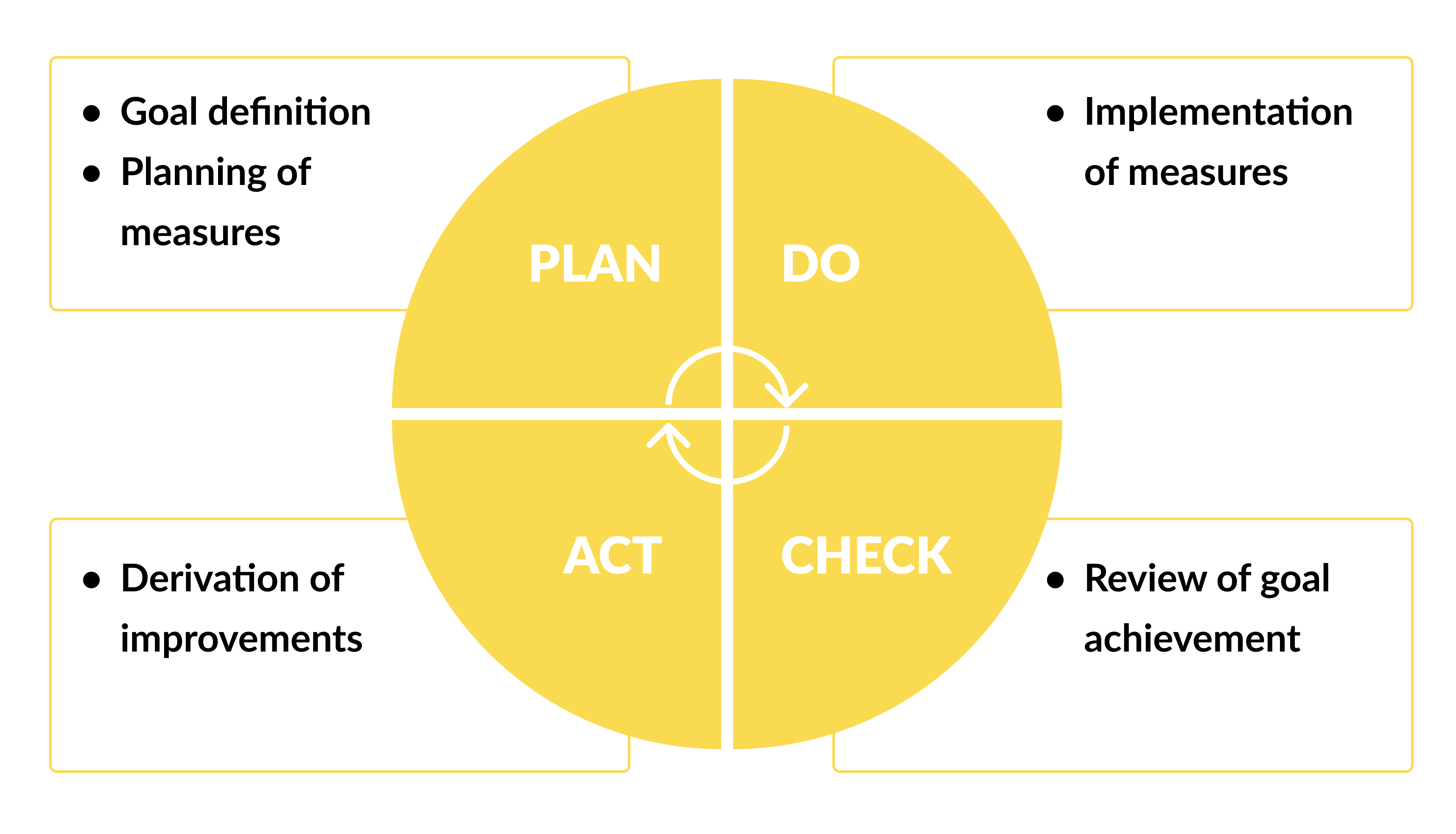
Despite its age, the PDCA cycle still finds its way into the processes of companies and organizations today. The Deming cycle can also be featured in connection with other methods, such as OKRs.
OKR is a goal-setting method for companies used at all organizational levels. The abbreviation stands for Objectives (O), or the value proposition for internal and external customers, and Key Results (KR), which measure whether a defined value proposition has been achieved.
When applying the OKR cycle from Workpath, a company is also going through a cycle similar to that of the PDCA.
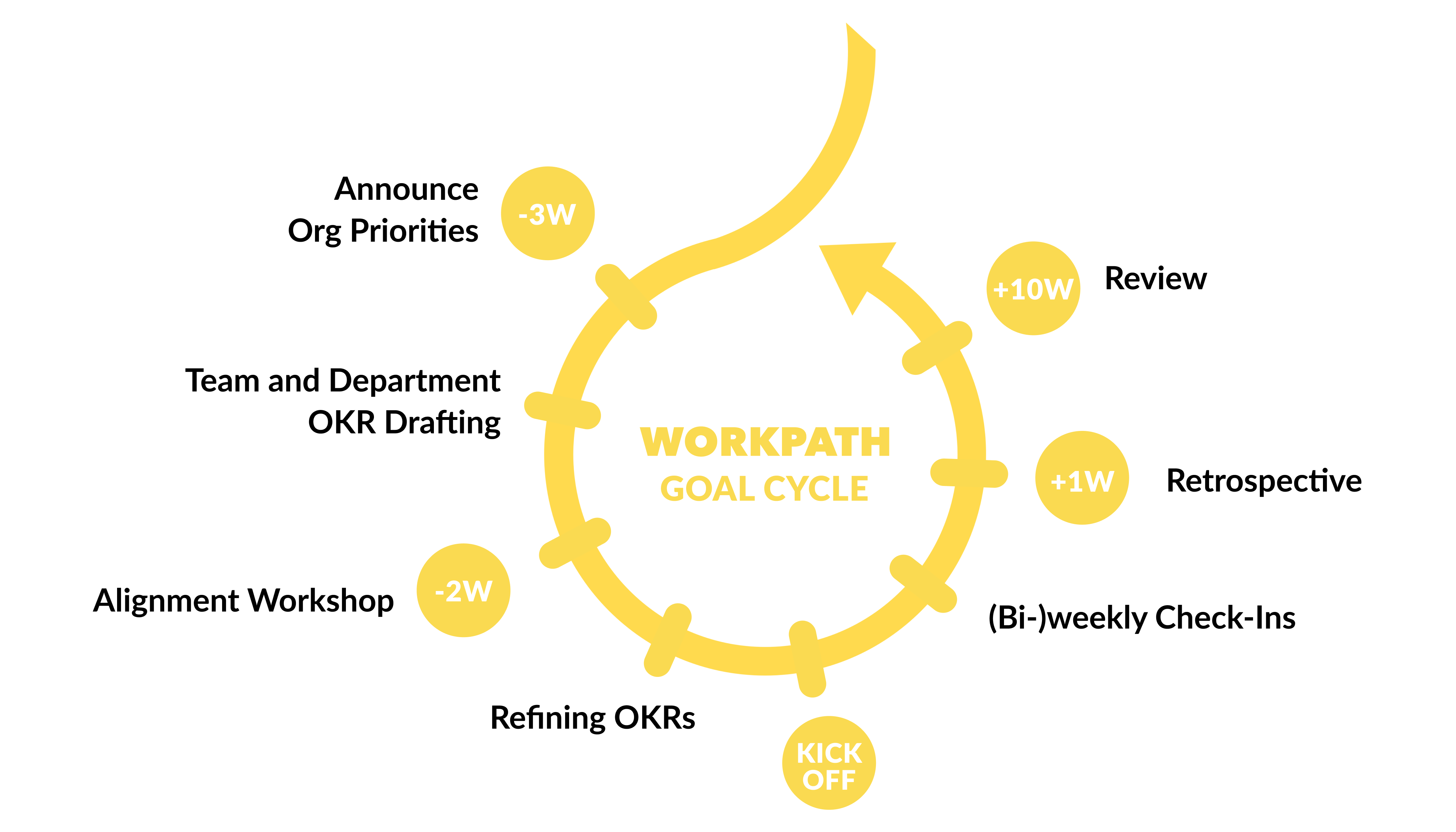
Based on the four stages of the Deming cycle, the OKR cycle’s individual steps are as follows:
PDCA cycle in Workpath goal cycle
Before the implementation of the OKR framework begins, the company’s management announces the priorities for the upcoming quarter, which provides a rough strategic direction for the cycle.
- Plan = Team OKR drafting
As a reminder, the first stage of the PDCA cycle includes the analysis of the desired state and the definition of respective actions. In an OKR implementation context, the individual teams and departments define their own goals and how they can contribute to the communicated priorities. The different OKRs are drafted at this time, which is one of the most important tasks of the cycle. After all, well-written Objectives and Key Results can be the deciding factor when it comes to success or failure.
In the Alignment Workshop that follows, all responsible individuals from each team discuss the predefined OKRs, prioritizing them more precisely and identifying specific dependencies. The final OKRs are then formulated within the teams.
- Do = OKR Kick-off
Final OKRs are then presented to all employees and the work beings. The focus throughout the entire quarter is placed on the tasks that contribute to the defined Objective. Short meetings are conducted during this time to ensure a short track for regular updates and discussions on insights and support possibilities.
- Check = Retrospective und review
Next, the processes around the OKRs and how they can be improved are discussed in a retrospective. Two weeks before the end of the cycle, all progress and success are documented and evaluated during a review. Would you like to know the differences between a retrospective and review? You can find out here.
- Act = Adjusting priorities and OKRs
OKRs that have not achieved the predefined goal or processes that require a certain amount of attention are then used in the subsequent OKR workshops to define new priorities and OKRs for the next cycle. The next cycle then begins.
The PDCA cycle comes with a variety of advantages and disadvantages organizations should be aware of before integrating it into their work processes. This prevents them from getting different results than expected.
Advantages of the PDCA cycle
- Integration of all employees
If an organization uses the PDCA cycle, all employees are automatically pulled into the project. This can have a positive impact on team chemistry and give employees a sense of belonging.
- Versatile application
The cycle can also be applied in many different ways. Not only can problem solving be simplified with the PDCA cycle, it can also be used in product manufacturing for both production and quality control.
- Unlimited application
In addition, unlimited application of the PDCA cycle is possible. As soon as it ends, the fourth and final stage directly sets the foundation for the new cycle. This leads to continuous process improvement.
Disadvantages of the PDCA cycle
Despite its advantages, PDCA is not perfect. There are also negative aspects to consider before deciding to apply the concept.
- A fixed principle
First and foremost, the PDCA cycle operates on a fixed principle and leaves little room for other variables during implementation.
- Slow progress
Since it has four stages, progress is also slow and quick results cannot be expected.
- Requires a lot of time
The cycle also requires a big time commitment, especially when it comes to planning and analyzing. Real actions do not take place often. If too much time is invested in analysis, projects can quickly come to a standstill.
What does PDCA mean?
The PDCA cycle is a concept for continuous improvement processes. PDCA is mainly used in product development and root cause failure analysis. The PDCA cycle consists of the four stages Plan, Do, Check and Act, which are completed one after the other in a fixed sequence to achieve the desired result.
What is the difference between PDCA and PDSA?
The only difference between PDCA and PDSA is the third stage. Instead of a “Check” stage, PDSA uses “Study.” This can be traced back to W. Edwards Deming, the developer of today’s version of the concept. Deming rejected the Check stage as, in his mind, the stage should focus on the learning effect and improvement of quality instead of comparison between the current and future state.
What are the individual stages of the cycle?
“Plan” refers to the first analysis of the current state and desired goal state. In the “Do” stage, the predefined actions for goal achievement are implemented. Next, the results from the actions are evaluated in the “Check” stage to determine if they led to goal achievement. In the final stage, the “Act” stage, satisfactory results are set as standard and results that fell short are used as starting points for the following cycle.
What are the advantages and disadvantages of PDCA?
The advantages of PDCA include the integration of all company team members, which has a positive effect on the atmosphere within the organization. The cycle is also versatile and has an unlimited number of applications. It can be useful for both failure analysis and product manufacturing, and can be repeated again after completion of the final stage. Disadvantages of PDCA lie mainly in its fixed structure of stages, which often provide little room for other ideas or variables. It also takes a lot of time to plan the concept because the four stages lead to slow progress.
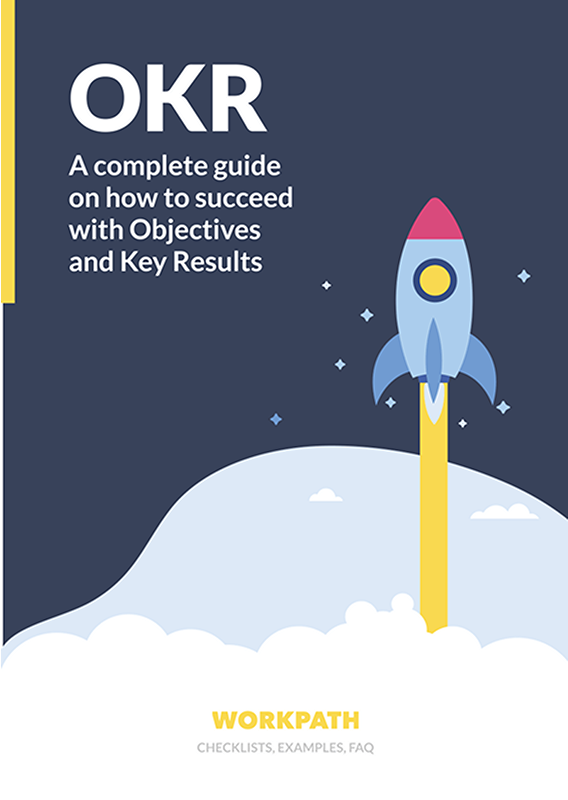